At its core, CNC milling entails the elimination of material from a workpiece through a series of collaborated motions. When the style is finished, the driver makes use of computer-aided production (CAM) software program to convert the CAD model right into a set of instructions that the CNC machine can read, usually in the type of G-code.
One of the standout attributes of CNC milling is its adaptability. Unlike conventional milling devices, which typically run along one or 2 axes, CNC milling makers can run on several axes simultaneously-- commonly 3, 4, or even five.
Discover cnc milling guide the transformative globe of CNC milling, an innovation that combines accuracy and automation to create premium components efficiently from numerous products, and discover its procedures, benefits, and essential considerations for success in modern-day production.
The choice of devices is an additional vital element of CNC milling. There is a variety of reducing tools readily available, consisting of end mills, face mills, and sphere mills, each suited for various applications. End mills, for instance, are versatile devices that can be utilized for side and face cutting, while ball mills are excellent for producing rounded edges and complicated curves. The suitable device choice can significantly influence the high quality of the finished item and the efficiency of the machining procedure. Furthermore, proper device maintenance and problem tracking play a significant duty in preserving optimal efficiency and prolonging device life.
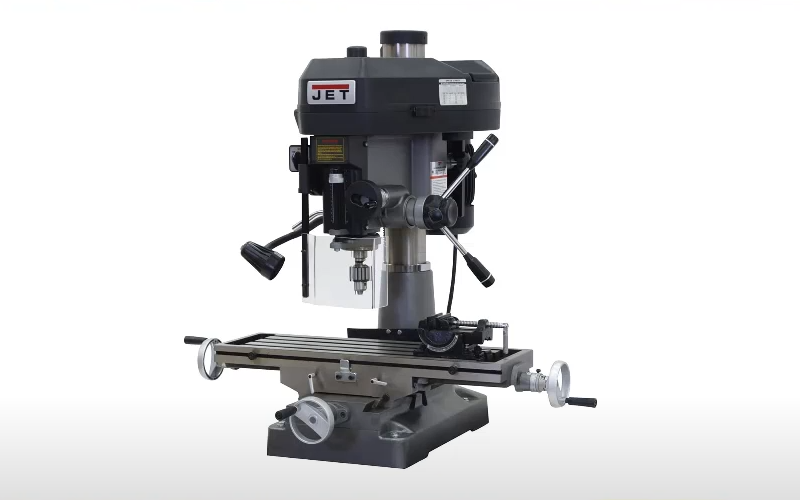
One essential variable to think about in CNC milling is material compatibility. Recognizing the residential or commercial properties of the product, including its hardness, machinability, and thermal conductivity, enables drivers to optimize the milling procedure and achieve exceptional outcomes while reducing wear and tear on devices.
Past the technological factors like style, tooling, and products, there are added considerations for optimizing CNC milling operations. Making use of innovative features such as toolpath optimization methods can simplify the milling process even more, making it possible for much faster machining cycles and reducing waste.
Additionally, among the significant advantages of CNC milling is the capability to automate recurring jobs, which minimizes human error and boosts manufacturing consistency. While typical milling machines require a competent driver to look after the manufacturing procedure, CNC milling machines can run unattended, performing pre-programmed directions with accuracy. This degree of automation not just enhances performance yet additionally frees up experienced workers from mundane tasks, enabling them to concentrate on better tasks such as quality assurance and procedure renovation.
Regardless of its advantages, transitioning to CNC milling is not without challenges. The schedule of renting options and inexpensive entry-level CNC milling machines has made it extra available for mid-sized and little companies to adopt this technology.
Training and ability growth for workers operating CNC milling machines are additionally necessary for optimizing the roi. Operators need a strong understanding of both the CNC machine itself and the software program being utilized for programming and monitoring. Several makers discover success by providing internal training programs or partnering with exterior training organizations to equip their groups with the needed skills and knowledge.
In current years, technological innovations continue to shape the area of CNC milling. As industries significantly turn to automation, incorporating functions such as man-made intelligence (AI) and maker knowing right into CNC makers can further boost the precision and performance of milling operations.
Developments in software program are continuously tightening the gap in between design and manufacturing. Modern CAD/CAM systems currently supply more user-friendly interfaces and enhanced simulation capabilities, enabling drivers to imagine machining procedures before they are carried out. By spotting possible issues in the layout phase, business can settle design flaws or enhance reducing techniques without sustaining expensive modifications to physical products.
In the context of CNC milling, sustainability is also getting relevance as producers try to find means to reduce their ecological influence. Executing techniques such as optimizing cutting criteria, using much more reliable tooling, and recycling materials can add to an extra sustainable milling operation. In addition, technologies such as additive manufacturing are being discovered along with CNC milling, presenting chances for hybrid production approaches that additionally boost sustainability by minimizing waste.
Discover benchtop milling machine the transformative world of CNC milling, an innovation that incorporates accuracy and automation to produce top notch parts efficiently from various materials, and uncover its processes, advantages, and crucial factors to consider for success in modern manufacturing.
In final thought, CNC milling stands for a crucial asset in contemporary production, supplying firms with the ability to produce complicated and premium parts successfully. Its combination of accuracy, convenience, and automation has actually made it a staple in industries ranging from aerospace to automotive, medical to consumer products. Comprehending CNC milling begins with a strong foundation in its processes, including the interplay between style, tooling, products, and software application. As innovation remains to progress, the possibility for proficient drivers to utilize these innovations will just increase, enabling better performances and innovations in CNC milling applications. By remaining educated on ideal techniques and arising modern technologies, suppliers can place themselves at the center of this vibrant market and completely make use of the abilities that CNC milling provides. Eventually, successful integration of CNC milling machinery, skilled labor force training, and clever automation leads the means for the future of production, where quality, efficiency, and sustainability become the hallmarks of functional quality.